Custom-Built Explosion Proof Sealers
Certified Explosion-Proof Vacuum Sealers for packaging in hazardous locations. Protection in locations where dangerous elements such as gases, combustible dust, and powder are present. Made in the USA.
Call For Pricing and Additional Information
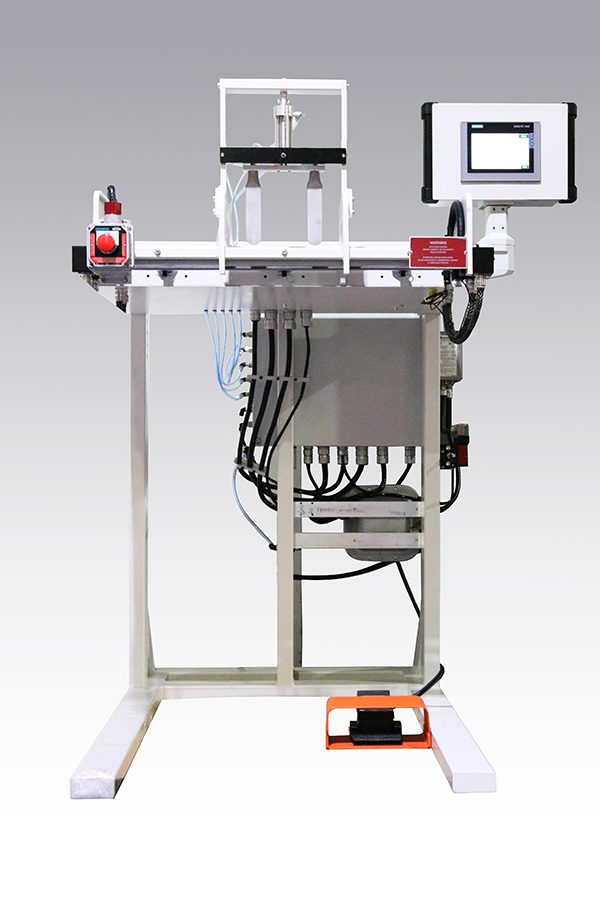
Explosion Proof Vacuum Sealers for HazLoc Settings
Custom sealing equipment built-in-accordance with explosion-proof safety standards for certification by US and European approval agencies. Validatable and cleanroom options are available and can be made in horizontal or vertical configurations with seal lengths up to 110” and beyond
IMPAK custom-produces highly advanced sealing equipment made for hazardous locations and materials. Our explosion proof vacuum sealers are custom designed to meet every element of certification required by your application and location.
“IMPAK worked backward from our certification specifications to produce equipment specifically made to meet our exact needs.” – Engineering Manager, Major Chemical Producer for U.S. DOD
Standard frame sizes from 18” to 110” are available with a vertical or horizontal orientation. Special configurations and sizes are available as required. Machines are made in the USA and can be produced for use in cleanrooms and HazLoc settings.
The advanced controllers on our heat sealers offer +/- 1-degree temperature accuracy. Results are measured, trackable and accurate, seal after seal.
IMPAK’s Explosion-Proof Sealers Come in Many Configurations:
Generally, requests for explosion-proof sealing equipment comes from businesses that require large frame industrial units, however, our expertise allows us to advise customers on any number of configurations and additional features. Our machines are built to exact customer specifications in Los Angeles, California.
HazLoc Sealing Equipment Explosion Proof Sealing Equipment Classified Location Sealers Explosion Proof Vacuum Sealer
Whether your need for an explosion-proof sealer is driven by your environment or your material to be packaged, IMPAK has the solution for your unique needs, no matter the industry. We’re prepared to work with you to create a system that safeguards you with standard features such as auto-shutoff and alarms, temperature runaway and vents, plus custom options depending on your needs.
IMPAK’s explosion-proof sealers can be made in any size and configuration and built to meet all class, division, and group requirements, and our robust control system makes them not only safe but arguably the most accurate explosion-proof sealers on the market. Contact our engineers to learn about our capabilities and get information based on your specific needs.
Options Include:
· Horizontal and Vertical Configurations
· Vacuum and Non-Vacuum Options
· State of the Art Controllers: iS2 System Available
· No Size Restrictions
· Frame Options: Include Powder Coated or Stainless Steel
· Cleanroom Ready: Options Available
· Calibration Service: Prior to Shipment
· Validatable: With Ports Included
· Temperature Controlled within +/- 1 degree
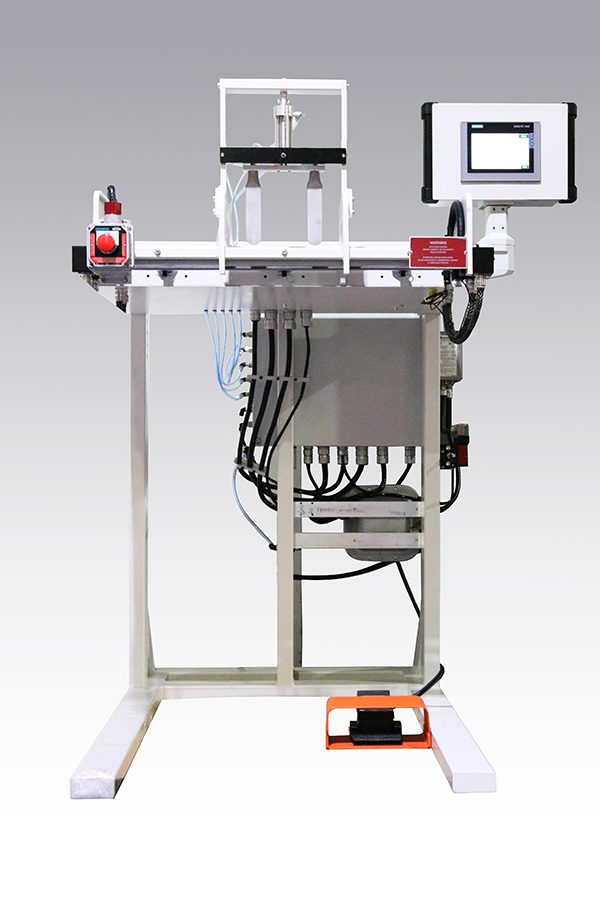
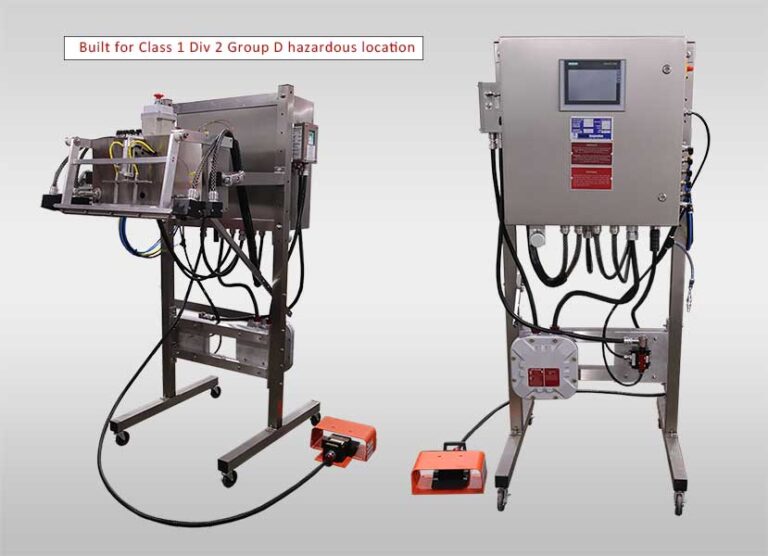
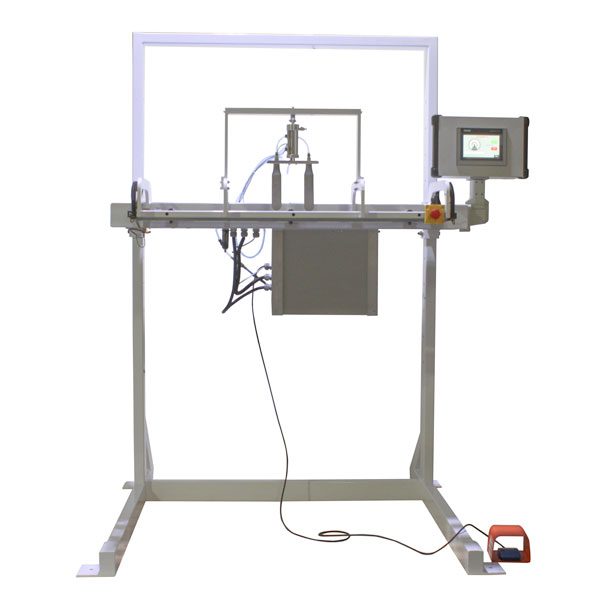
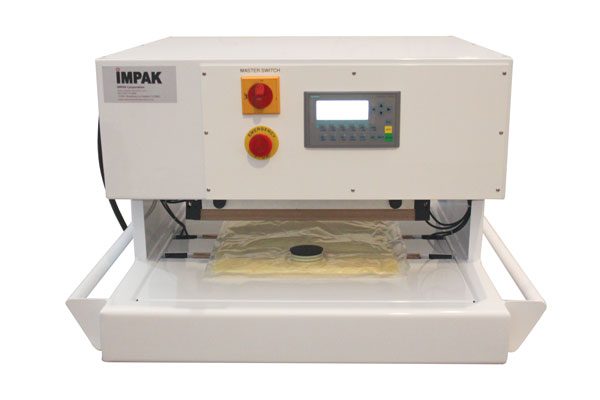
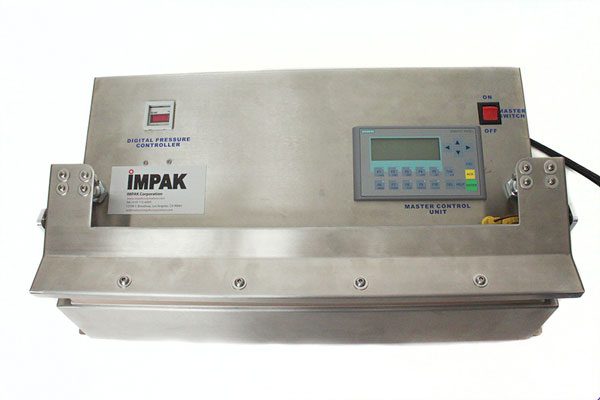
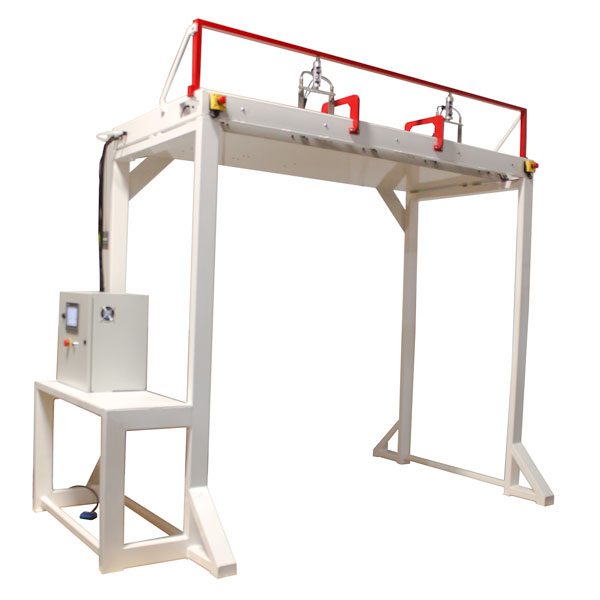
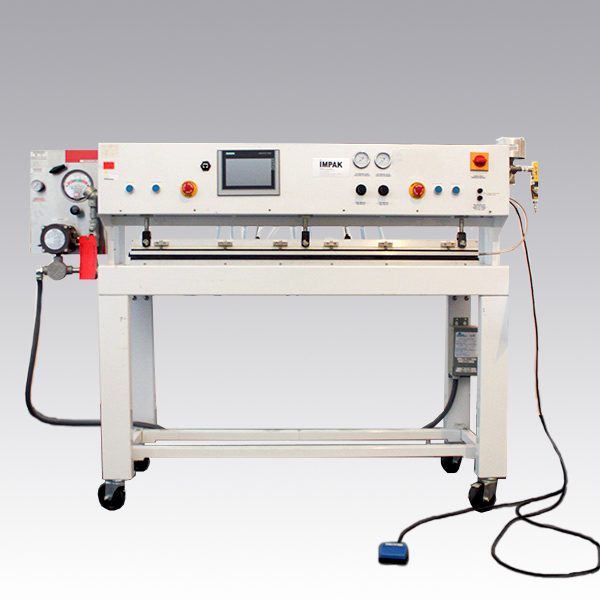
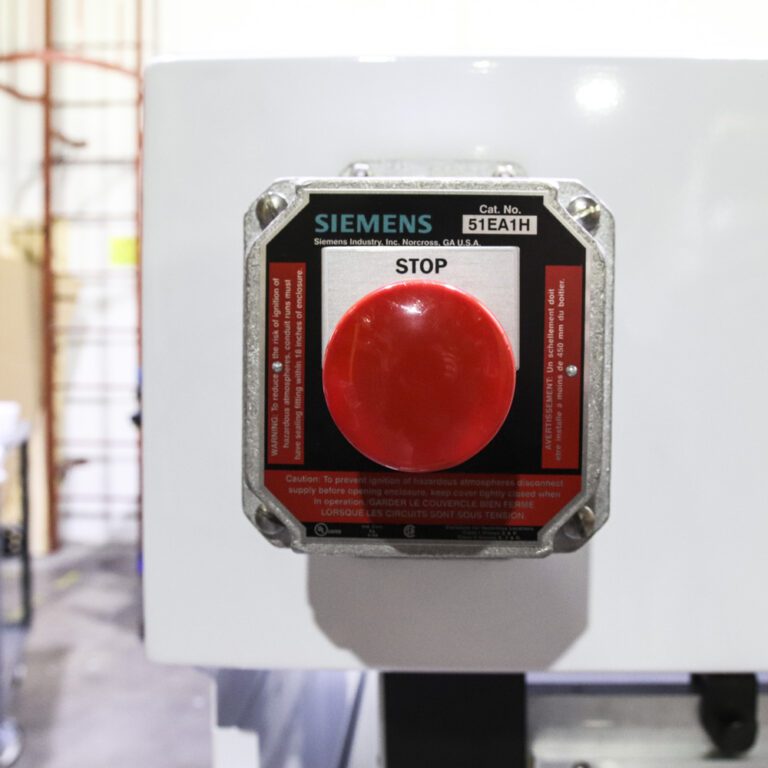

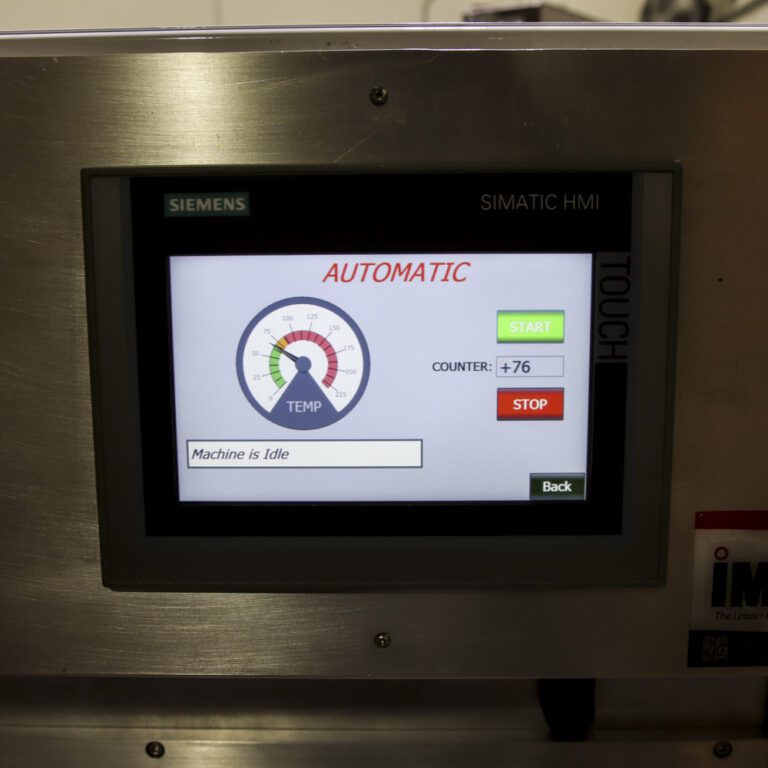
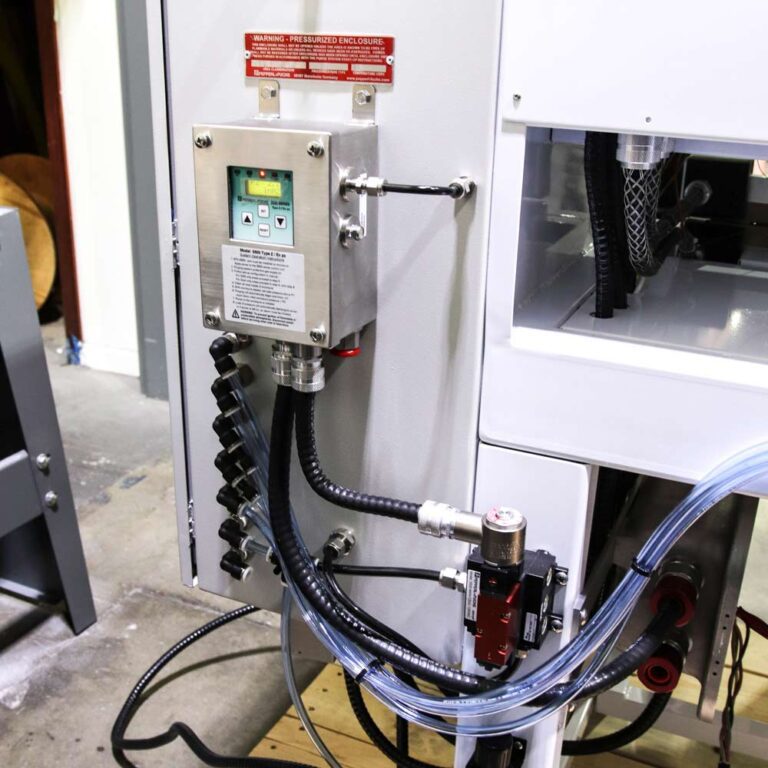
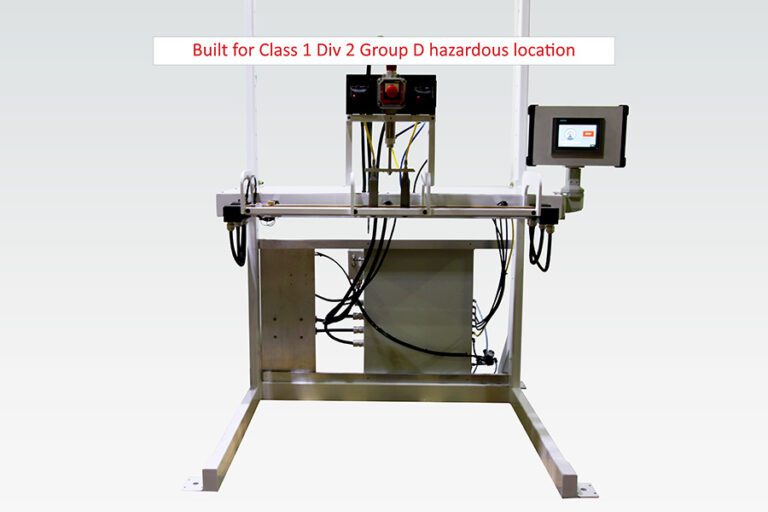
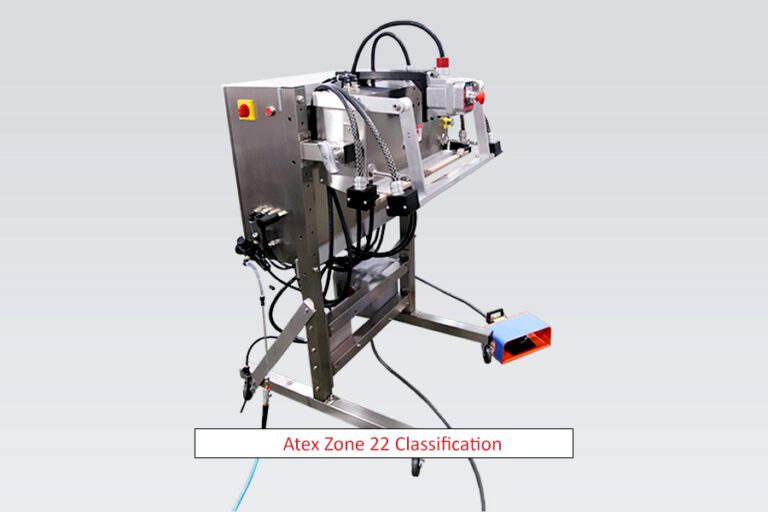
“Built-in-Accordance” vs. Certified Explosion Proof
For quality purposes, we always recommend third-party certification. We know this puts us in a unique position among machine manufacturers as we have competitors that have produced machinery without even once using a third-party certification.
Class I Locations – Flammable Gas Settings
Locations classified as Class I are locations where there are flammable gases or vapors in the air, such as natural gas or gasoline vapor which are deemed as hazardous for their potential for accidental ignition. When such materials are present in the atmosphere, there is a combustion potential. An explosion can result from electrical and non-electrical sources, which are harmless under other conditions but of extreme danger in a setting where combustible gases are present. Electrical arcs become a source of danger in this type of hazardous location.
All of these Class I hazardous locations require very special equipment and operator training created specifically for use in Class I hazardous locations.
Class I locations include:
- Aircraft hangars
- Fuel servicing areas
- Dry cleaning plants
- Spray painting facilities
- Commercial garages
- Bulk storage plants
- Areas with liquefied petroleum
- Areas with natural gas
Article 100 of the NEC describes an Explosion-Proof Apparatus as being “enclosed in a case that is capable of withstanding an explosion of a specified gas or vapor that may occur within it and of preventing the ignition of a specified gas or vapor surrounding the enclosure by sparks, flashes, or explosion of the gas or vapor within, and which operates at such an external temperature that a surrounding flammable atmosphere will not be ignited thereby.”
Class II Locations – Combustible Dust Settings
The second type of hazardous location is an area made dangerous by the presence of combustible materials, which may be suspended in the atmosphere. These combustible dusts can cause powerful explosions. While normally harmless, dust may collect in, or near electrical equipment and can interfere with the safe dissipation of heat from electrical equipment, or could be ignited by the operation of electrical equipment.
Class II locations include:
- Grain elevators
- Flour and feed mills
- Plants with magnesium or aluminum powder
- Medicine manufacturing plants
- Producers of starch or candies
- Sugar and cocoa processing plants
- Locations with fireworks
- Coal plants and other carbon handling areas

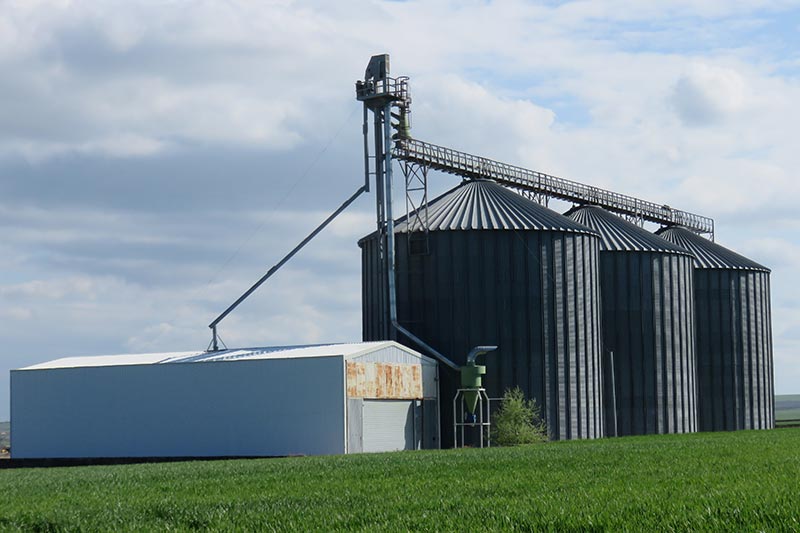
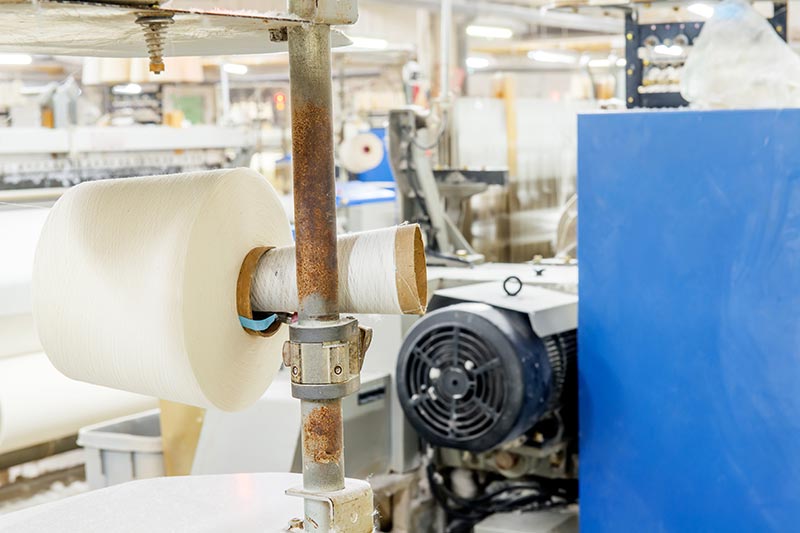
Class III Locations – Ignitable Fibers
Locations classified as Class III are areas where easily ignited fibers are present. Unlike gases and dust, fibers are unlikely to be suspended in the air but cause danger when they collect around machinery or on electrical fixtures and where heat, a spark, or exposure to hot metal can ignite them.
Class II locations include:
- Textile mills and clothing manufacturing plants
- Plants with cut wood and heavy sawdust
- Paper recycling facilities